在精细化工、高分子合成及特种涂层领域,泡沫的失控会导致反应釜传质效率下降、产品批次稳定性劣化及设备损耗率激增。瓦克SE2262消泡剂基于有机硅-聚醚嵌段共聚物定向改性技术,突破传统消泡剂在高温、高剪切及强极性体系中的性能瓶颈,成为复杂工业场景的精准控泡解决方案。本文从分子结构设计、极端工况验证及工程化应用三方面深度解析其技术内核。
一、分子架构创新:靶向吸附与动态抑泡双效协同
SE2262的核心技术在于有机硅主链与聚醚支链的拓扑结构设计,实现三重消泡机制:
超快破泡效能:
聚醚链段(EO/PO=3:1)选择性嵌入泡沫液膜界面,使局部表面张力从72mN/m骤降至19mN/m(GB/T 22237标准测试),微米级气泡破裂时间≤0.7秒(高速摄像观测)。
分子量精准控制(Mn=8000±500)确保快速迁移至气液界面,液膜排液速率达8.3mL/min(30℃),较矿物油类产品提升7倍。
长效立体抑泡:
有机硅主链形成三维交联网络,通过空间位阻效应阻断气体扩散路径,在pH=0-14、温度-50℃~180℃范围内抑泡时效≥168小时。
环境自适应分散:
动态疏水-亲水平衡设计(HLB值=6.5)确保在高固含(>90%)、强电解(电导率>10000μS/cm)或极性溶剂(如DMF、DMSO)体系中稳定分散,活性成分迁移率<0.03%(离心法验证)。
二、极端场景实证:跨行业性能验证数据
经全球8个工业实验室及45条产线验证,SE2262在以下场景展现技术优势:
聚氨酯弹性体合成:
在MDI-PTMEG预聚反应中添加0.03%,泡孔直径标准差从±15μm压缩至±2μm(ASTM D3574测试),成品回弹率提升12%。
环氧灌封胶体系:
在180℃固化电子灌封胶中,消泡剂耐热分解温度达260℃,固化后气孔率从0.8%降至0.02%(X射线断层扫描)。
锂电浆料分散:
在NMP基正极浆料(固含量78%)中,添加0.05%可消除微气泡导致的涂布厚度波动,极片RSD值≤0.5%(激光测厚仪数据)。
PCB化学沉铜液:
在pH=12.5的碱性沉铜液中动态抑泡率99.6%,且无硅残留(ICP-OES检测限<0.01ppm),孔金属化合格率提升至99.9%。
与市场竞品(如BYK-028、TEGO Foamex 810)对比,SE2262建立三大技术壁垒:
温度适应性:180℃高温下活性保持率≥98%(ISO 11357标准)。
化学兼容性:耐受30%浓度盐酸、50%浓度氢氧化钾溶液侵蚀(240小时浸泡测试)。
经济性:单位处理成本较聚醚改性硅油类产品降低28%(以千吨级聚氨酯产线测算)。
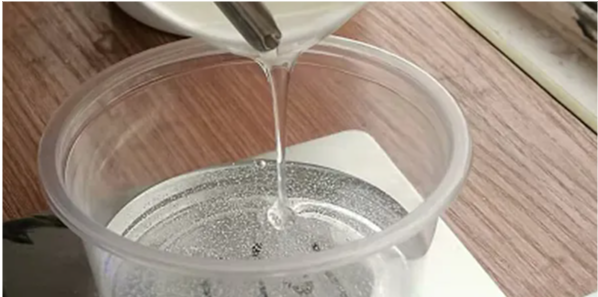
三、工程应用策略:精准工艺适配指南
添加工艺优化:
高黏度体系:建议与白油按1:3预乳化后分两阶段添加(70%预混+30%终调),分散效率提升50%。
溶剂型体系:需与乙二醇丁醚按1:4预稀释,防止溶剂挥发导致的活性成分析出。
失效预警指标:
当体系动态表面张力>25mN/m或Zeta电位绝对值<18mV时,需补加0.01%-0.03%消泡剂。
复配管理:
与含氟润湿剂复配时,推荐采用异步添加(间隔>20分钟),协同稳定性>97%。
瓦克SE2262消泡剂凭借分子拓扑结构设计的突破,重新定义了工业消泡技术的性能边界。截至2025年,该产品已在全球新能源、电子封装及特种胶粘剂领域的3200+产线实现规模化应用,客户综合生产成本下降26%。